Proces produkcji profili stalowych giętych na zimno
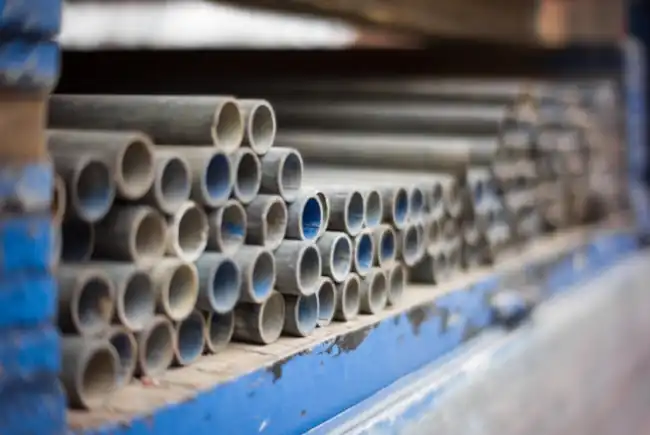
Profile te powstają w wyniku formowania blachy lub taśmy stalowej w temperaturze pokojowej, co pozwala uzyskać elementy o wysokiej dokładności wymiarowej, gładkiej powierzchni i zwiększonej odporności na obciążenia mechaniczne. Dzięki swojej trwałości i różnorodności kształtów, profile gięte na zimno znajdują zastosowanie w wielu branżach, takich jak budownictwo, motoryzacja czy przemysł maszynowy.
Wybór odpowiedniego surowca
Najczęściej stosuje się stal konstrukcyjną o różnych gatunkach, takich jak S235, S355 czy S500, które charakteryzują się wysoką odpornością na obciążenia i łatwością w obróbce. W zależności od przeznaczenia profili, dobiera się stal o odpowiednich właściwościach chemicznych i mechanicznych, uwzględniając wymagania dotyczące wytrzymałości, elastyczności czy odporności na korozję.
Surowiec w postaci blachy lub taśmy stalowej musi być wolny od wad powierzchniowych, takich jak pęknięcia, wtrącenia czy zanieczyszczenia, które mogłyby osłabić gotowy profil. Przed przystąpieniem do procesu formowania, stal jest dokładnie przygotowywana, co obejmuje jej oczyszczenie, sprawdzenie wymiarów oraz kontrolę jakości, aby zapewnić najwyższą precyzję i trwałość finalnych produktów.
Proces formowania profili stalowych na zimno
Proces formowania profili stalowych na zimno polega na kształtowaniu blachy lub taśmy stalowej w temperaturze pokojowej przy użyciu specjalistycznych maszyn formujących, takich jak walcarki i prasy. Materiał przechodzi przez szereg rolek formujących, które stopniowo nadają mu pożądany kształt, taki jak profil okrągły, kwadratowy, prostokątny czy owalny. Proces ten wymaga dużej precyzji, ponieważ każde odchylenie od normy może wpłynąć na jakość i parametry końcowego produktu.
Formowanie na zimno pozwala na uzyskanie profili o wysokiej wytrzymałości, gładkiej powierzchni i jednolitej strukturze, a także zmniejsza ryzyko występowania odkształceń i niedoskonałości. Dodatkowo, taki proces zwiększa twardość stali i poprawia jej odporność na obciążenia mechaniczne, co jest szczególnie ważne w przypadku elementów konstrukcyjnych. Dzięki zaawansowanym technologiom możliwe jest również precyzyjne kontrolowanie wymiarów profili, co gwarantuje ich powtarzalność i zgodność z wymaganiami projektowymi.
Cięcie i obróbka końcowa
Po zakończeniu procesu formowania, profile stalowe przechodzą do etapu cięcia i obróbki końcowej, który ma na celu dostosowanie ich do określonych wymagań projektowych. Cięcie odbywa się przy użyciu specjalistycznych maszyn tnących, takich jak piły taśmowe, przecinarki lub nożyce gilotynowe, które zapewniają precyzyjne dopasowanie długości profili zgodnie ze specyfikacją klienta. W przypadku bardziej skomplikowanych konstrukcji, profilom mogą być nadawane dodatkowe kształty, a także wykonywane otwory montażowe, fazowanie krawędzi czy frezowanie.
Niezwykle istotnym elementem obróbki końcowej jest usuwanie zadziorów i wygładzanie krawędzi, co zwiększa bezpieczeństwo użytkowania i ułatwia dalszy montaż. Na tym etapie profile są również poddawane kontroli jakości, obejmującej sprawdzenie wymiarów, geometrii oraz powierzchni, aby upewnić się, że spełniają wszystkie normy i wymagania techniczne. Dzięki starannej obróbce końcowej, gotowe profile są w pełni przygotowane do dalszych etapów produkcji lub bezpośredniego montażu.
Zabezpieczenie profili stalowych przed korozją
Jedną z najczęściej stosowanych metod ochrony jest cynkowanie ogniowe, polegające na zanurzeniu profilu w płynnym cynku, który tworzy na jego powierzchni trwałą warstwę ochronną. Alternatywnym rozwiązaniem jest cynkowanie galwaniczne, które zapewnia cieńszą, ale równie estetyczną powłokę, odpowiednią dla elementów wykorzystywanych w mniej wymagających warunkach.
W przypadku profili przeznaczonych do środowisk o zwiększonej wilgotności lub agresywnych warunkach atmosferycznych stosuje się także powłoki lakiernicze, które dodatkowo wzmacniają ochronę antykorozyjną i poprawiają wygląd elementu. W niektórych przypadkach łączy się różne metody zabezpieczenia, na przykład cynkowanie z późniejszym malowaniem proszkowym, co pozwala osiągnąć maksymalną odporność na działanie czynników zewnętrznych.